- #1
greg_rack
Gold Member
- 363
- 79
- Homework Statement
- Plates are made up of Aluminum(given max shear strength), nails are of given maximum shear force. Dimensions and load intensity are given. What will fail first, among the two plates and the nails?
DIAGRAM SHOWN BELOW
- Relevant Equations
- Shear formula
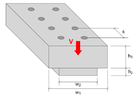
Hi guys, this is an exercise I have been tasked to solve for an assignment. First of explaining you what I have done to solve it using the shear equation, in order to find the maximum shear stress and the shear flow in the juncture, one big question:
how is it legal to utilize the shear formula in this case? One big limitation of it is given by the "aspect ratio" of the cross section; since to derive it the assumption of uniform shear distribution along the width has to be made, actual transverse stresses for flat cross sections(for this specific case, w1/h1 is approx. 4, whilst the threshold should be approx. 0.5) deviate significantly from the values predicted by the equation, since stress is not uniform along the width.
Thus, does the problem I've been given with even make sense? I'm quite confused